Understanding Plastic Injection Mold Tooling: A Comprehensive Guide
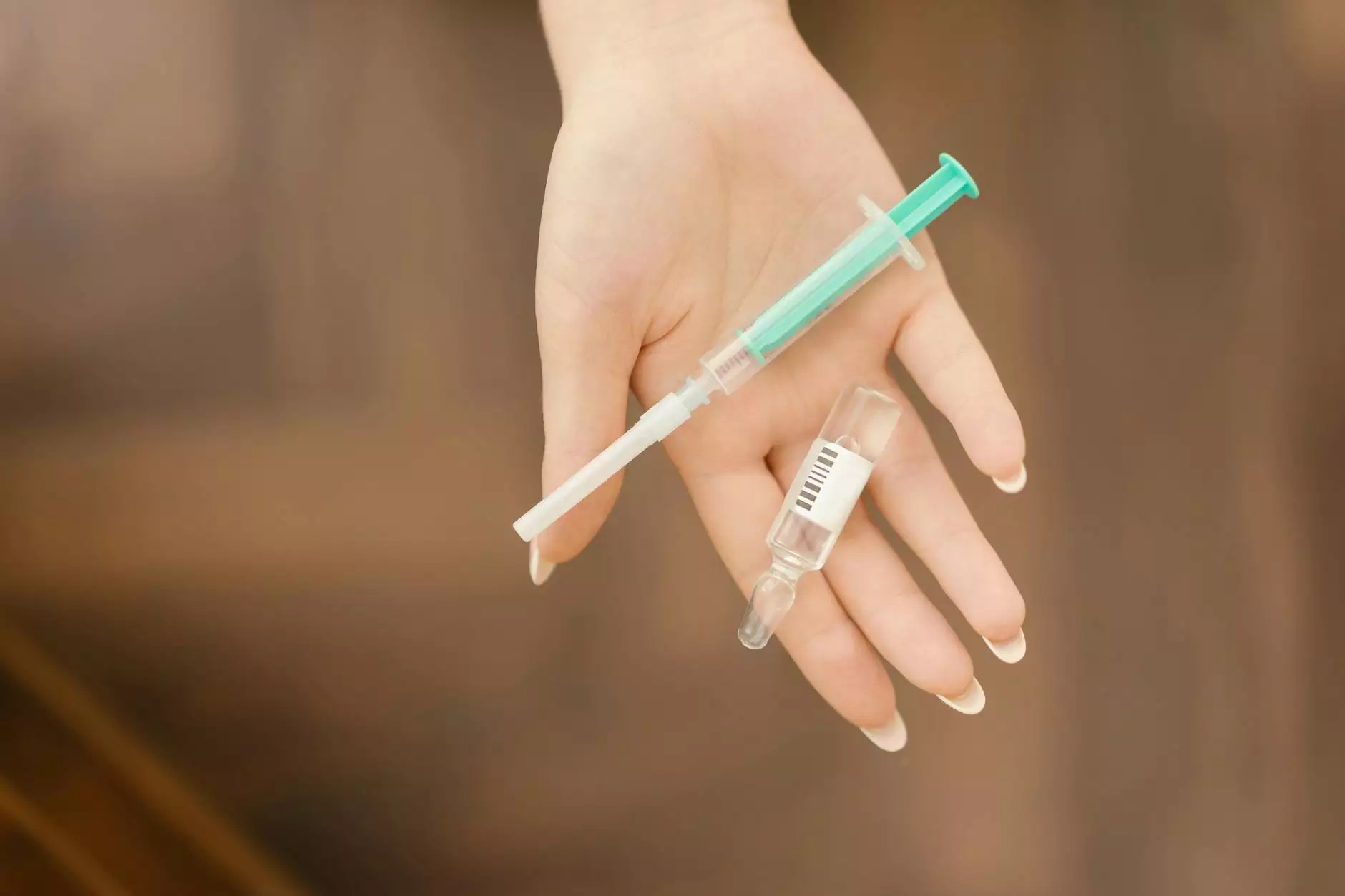
Plastic injection mold tooling is a critical component in the manufacturing industry, enabling the production of intricate and precise plastic parts. This process is not only essential for mass production but also significantly enhances the quality and efficiency of manufacturing. In this article, we will delve into the various aspects of plastic injection mold tooling, highlighting its importance in metal fabrication, and how businesses like DeepMould are leading the charge in providing exceptional tooling solutions.
The Basics of Plastic Injection Mold Tooling
At its core, plastic injection molding is a manufacturing process used to create plastic parts by injecting molten plastic into a mold. The mold is designed with precise specifications to shape the final product. Here are the key components of the injection molding process:
- The Injection Unit: This component is responsible for melting the plastic and injecting it into the mold.
- The Clamping Unit: This secures the mold during the injection process to ensure it remains closed under pressure.
- The Mold: Custom-designed to create the desired shape of the product, molds are typically made from durable materials like steel or aluminum.
Why Choose Plastic Injection Mold Tooling?
Plastic injection mold tooling offers a myriad of advantages, making it a preferred choice for manufacturers across multiple industries:
- High Efficiency: The process allows for rapid production, making it ideal for mass manufacturing.
- Cost-Effectiveness: Although the initial costs for mold creation can be high, the long-term savings in production costs are significant.
- Precision and Quality: The molds enable consistent quality and highly detailed designs, which can be challenging to achieve with other manufacturing methods.
- Material Versatility: A wide variety of plastics can be used, making it suitable for different applications.
Applications of Plastic Injection Mold Tooling in Metal Fabrication
Plastic injection mold tooling plays an essential role in the metal fabrication category of business as it complements the use of metal parts with custom plastic components. Here are a few applications:
1. Prototyping
In the early stages of product development, rapid prototyping using plastic injection mold tooling allows companies to test designs and iterate quickly, reducing time to market.
2. Automotive Industry
The automotive sector relies heavily on plastic components, from dashboards to exterior fittings. Molded parts contribute to vehicle lightweighting, enhancing fuel efficiency.
3. Consumer Electronics
Devices such as smartphones and laptops incorporate numerous plastic components, making precise molding vital for aesthetics and functionality.
4. Medical Devices
In the medical field, durability and precision are paramount. Injection molded parts are used for everything from syringes to complex devices, ensuring safety and reliability.
The Process of Plastic Injection Mold Tooling
Understanding the detailed process of plastic injection mold tooling is essential for appreciating its efficiency and effectiveness:
Step-By-Step Process
- Design: The process begins with a detailed design of the mold using CAD software. This design will determine the final shape and dimensions of the product.
- Material Selection: Choosing the right plastic material is crucial based on the application and desired properties, such as strength and flexibility.
- Mold Fabrication: This step involves creating the mold, typically through CNC machining or EDM (Electrical Discharge Machining) to achieve high precision.
- Molding: Once the mold is ready, the plastic is heated until it becomes liquid and then injected into the mold under high pressure.
- Cooling: After the mold fills, it cools, solidifying the plastic into the desired shape. This cooling phase is critical for ensuring the dimensional stability of the part.
- Finishing: Post-molding processes, such as trimming excess material, can be done to ensure that the final product meets specifications.
Advantages of Working with DeepMould
When it comes to plastic injection mold tooling, DeepMould stands out as a leader in the industry. Here are several reasons why
- Expertise: Our team consists of experienced professionals who have extensive knowledge in designing and producing high-quality molds.
- State-of-the-art Technology: We utilize cutting-edge technology and equipment to ensure precision and efficiency in our mold making process.
- Custom Solutions: We specialize in understanding client needs and creating tailored solutions that fulfill specific requirements.
- Quality Assurance: Stringent testing and quality control measures guarantee that our molds meet the highest industry standards.
- Timely Delivery: We prioritize meeting deadlines and provide prompt services without compromising quality.
The Future of Plastic Injection Mold Tooling
The landscape of plastic injection mold tooling is continuously evolving, influenced by advancements in technology, materials, and manufacturing processes. Some key trends shaping the future include:
1. Sustainable Practices
With increasing focus on sustainability, manufacturers are seeking ways to reduce waste and energy consumption. Innovations in biodegradable plastics and recycled materials are becoming significant in mold tooling.
2. Automation and Robotics
The integration of automation and robotics into the injection molding process enhances productivity, reduces labor costs, and improves safety in manufacturing environments.
3. Smart Manufacturing
Industry 4.0 technologies are paving the way for smarter production facilities where data analytics, IoT (Internet of Things), and machine learning optimize the molding process.
Conclusion
In summary, plastic injection mold tooling remains an indispensable aspect of modern manufacturing, significantly contributing to the efficiency and quality of produced goods. DeepMould is committed to providing outstanding tooling solutions, ensuring that businesses achieve their production goals while maintaining high standards of quality and innovation. By staying abreast of industry advancements and focusing on sustainability, we are poised to meet the evolving demands of our clients.
For businesses in the metal fabrication sector, harnessing the power of plastic injection mold tooling is not just a choice—it’s a strategic advantage that can drive success and growth. Whether you need a single prototype or an extensive production run, partnering with an experienced provider like DeepMould is essential to navigate the complexities of the market and emerge as a leader.