Understanding Tube Fitting Dimensions for Optimal Performance
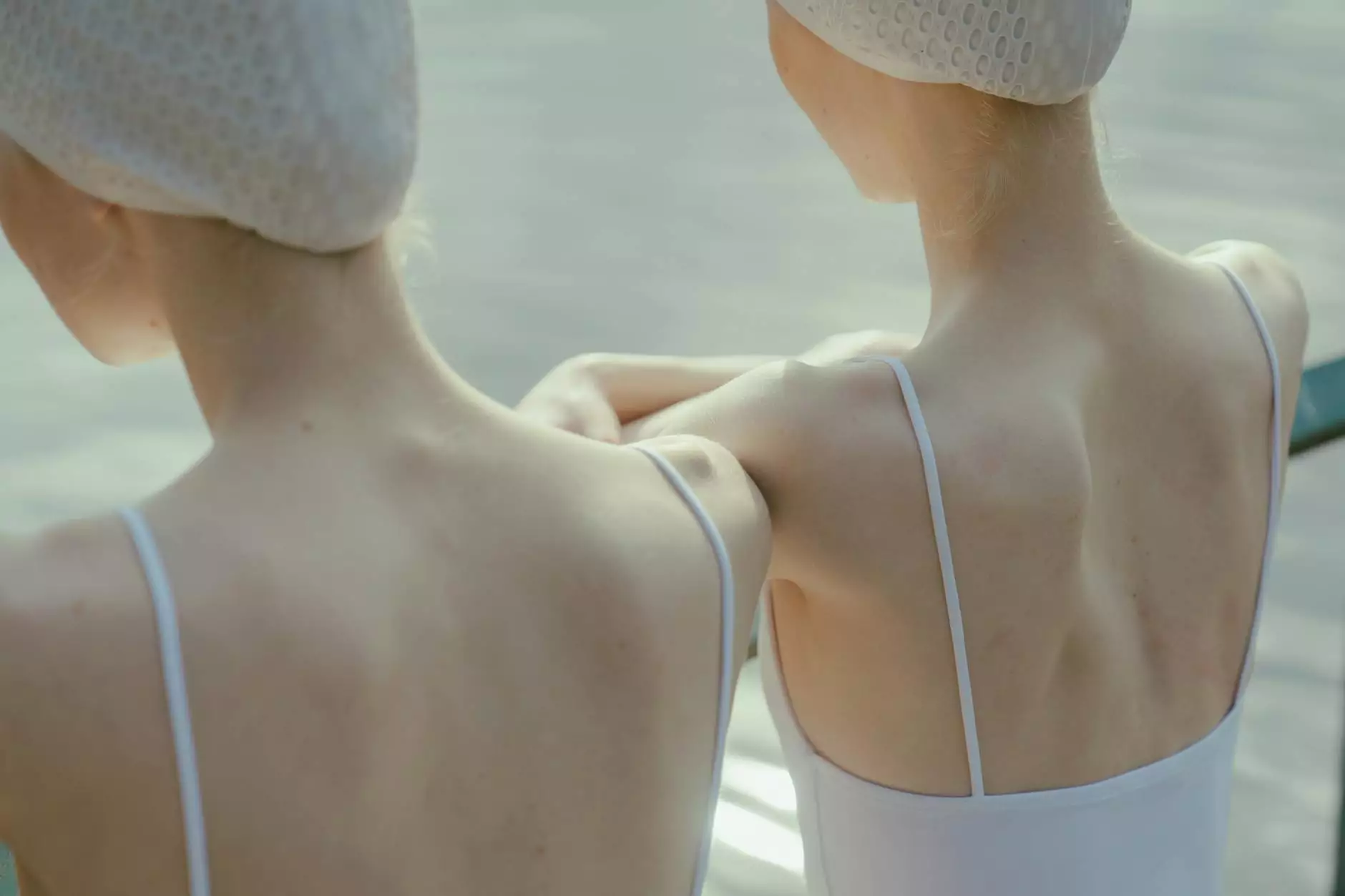
Tube fitting dimensions play a crucial role in ensuring that fluid and gas systems operate efficiently and reliably. The accurate measurement and correct selection of tube fittings can prevent leakage, reduce maintenance costs, and ensure the longevity of piping systems. This comprehensive guide delves deep into the importance of tube fitting dimensions, their types, and how they relate to other components in a piping system.
The Importance of Tube Fitting Dimensions
In any industrial or commercial piping system, tube fittings are essential components that help connect different sections of tubing, pipes, or hoses. Understanding the dimensions of tube fittings is crucial for several reasons:
- Leak Prevention: Properly sized fittings ensure a tight seal, minimizing the risk of leaks in high-pressure systems.
- System Compatibility: Correct dimensions ensure that fittings are compatible with existing tubing, preventing installation issues.
- Flow Efficiency: The correct sizing allows fluids to flow efficiently without unnecessary restrictions, maintaining optimal pressure levels.
- Ease of Installation: Accurate dimensions simplify installation procedures, allowing for quicker assembly and reducing labor costs.
Types of Tube Fittings
There are various types of tube fittings, each designed for specific applications. Understanding these fittings and their dimensions is vital for selecting the right components for your system. The following categories will cover the most commonly used tube fittings:
1. Ferrule Fittings
Ferrule fittings are essential in many hydraulic and pneumatic systems. They consist of a body, a ferrule, and a nut. The dimensions of ferrule fittings are critical for achieving the right compression seal. Common materials include stainless steel and brass, chosen for their durability and corrosion resistance.
2. Forged Pipe Fittings
Forged pipe fittings are created through a process that enhances the mechanical properties of the metal. The dimensions of these fittings are important to ensure strength and compatibility with the piping system. Typical forging materials include carbon steel and alloy steel.
3. Threaded Pipe Fittings
Threaded pipe fittings use threads to create a mechanical seal. Knowing the thread dimensions such as NPT (National Pipe Thread) is crucial for a secure fit. They are typically used in low-pressure applications, where ease of assembly and disassembly is desired.
4. Flanges
Flanges provide a robust connection point between pipes, valves, or other equipment. Their dimensions include the outer diameter and bolt hole sizes, which must match corresponding flanges to ensure a secure fit and prevent leaks.
5. Check Valves
Check valves prevent backflow in a piping system. The dimensions of check valves must accommodate the flow direction while ensuring that the valve opens under sufficient pressure conditions. Proper sizing is crucial for effective operation.
6. Ball Valves
Ball valves are used for on/off control in fluid systems. The dimensions of the valve body, stem, and ball must be precisely manufactured to ensure a tight shut-off and minimal flow resistance when open.
7. Needle Valves
Needle valves allow for fine adjustments in fluid flow. Their dimensions must allow for precise control over flow rates, making them exceptional for applications requiring detailed regulation.
8. Manifold Valves
Manifold valves serve as a central point to control multiple fluid pathways. Accurate dimensions are required to ensure that all connections are secure and leak-free.
9. Double and Single Ferrule Tube Fittings
These fittings utilize one or two ferrules respectively to create a secure seal around the tube. The dimensions specifically refer to the size of the tube and the width of the ferrules, impacting the reliability of the connection.
10. NPT Fittings
NPT fittings rely on tapered threads to create a seal. Understanding the dimensions of NPT fittings, including nominal sizes and taper angles, is crucial for ensuring a proper fit in applications ranging from plumbing to gas lines.
How to Measure Tube Fitting Dimensions
Accurate measurement of tube fitting dimensions involves several key considerations:
- Outside Diameter (OD): Measure the outer diameter of the tube using calipers for precise accuracy.
- Inside Diameter (ID): The inside diameter can be critical for flow calculations; use a bore gauge for accurate measurement.
- Wall Thickness: Knowing the wall thickness of the tube allows for proper selection of fittings.
- Length of Fittings: For threaded fittings, ensure to measure the length required for the application.
- Flange Dimensions: Flange size encompasses diameter and bolt hole patterns; both must match for a secure connection.
Common Materials Used in Tube Fitting Manufacturing
Different materials provide varying properties that affect fitting dimensions and their overall functionality. Here are some common materials:
- Stainless Steel: Known for its corrosion resistance and strength, commonly used in chemical processing.
- Brass: Offers excellent machinability and corrosion resistance, ideal for low-pressure applications.
- Carbon Steel: Provides high strength and is cost-effective, often used in heavy-duty applications.
- Plastic: Lightweight and resistant to various chemicals, suitable for low-pressure systems.
Calculating Flow Rates with Tube Fitting Dimensions
Understanding how tube fitting dimensions affect flow rates is crucial for designing efficient systems. The flow rate through a pipe is influenced by:
- Diameter of the Pipe: A larger diameter facilitates higher flow rates.
- Length of the Pipe: Longer pipes create more friction, reducing flow.
- Type of Fluid: Viscosity plays a significant role in how fluid flows through fittings.
- Temperature: Higher temperatures can reduce viscosity, increasing flow rates.
Best Practices for Selecting Tube Fittings
Selecting the right tube fittings requires understanding various factors that impact their performance:
- Determine System Pressure: Ensure the fittings can withstand the maximum operating pressure.
- Assess Material Compatibility: Choose materials suitable for the fluids used in order to avoid corrosion or degradation.
- Identify Required Dimensions: Accurately measure the required tube fitting dimensions for a perfect fit.
- Follow Manufacturer Specifications: Always refer to manufacturer recommendations for optimal performance.
Troubleshooting Common Issues with Tube Fittings
Fitting issues can lead to significant operational problems. Here are some common problems and solutions:
- Leakage: Check for the correct fitting dimensions and whether the fittings were installed properly.
- Excessive Vibration: Ensure adequate support is provided for the piping system to minimize vibration.
- Corrosion: Regularly assess the fittings for signs of wear and choose compatible materials.
- Pressure Drop: Verify that no fittings are undersized or partially blocked, which can restrict flow.
Conclusion
In conclusion, understanding tube fitting dimensions is paramount for anyone involved in the design, maintenance, or operation of piping systems. With an array of fitting types, materials, and measurement techniques available, professionals can ensure optimal performance, safety, and reliability in their fluid handling systems. By considering the detailed information provided above, including best practices for selection and common troubleshooting tips, you can make informed decisions that serve the long-term interests of your organization.
For more information on quality fittings and their dimensions, visit techtubes.in. Here, you will find a comprehensive selection of products ranging from tube fittings to valves, all designed for your specific engineering needs. Equip your operations with the best-fitting solutions today!