Ultimate Guide to Metal Cutting Machines (Máy Cắt Kim Loại)
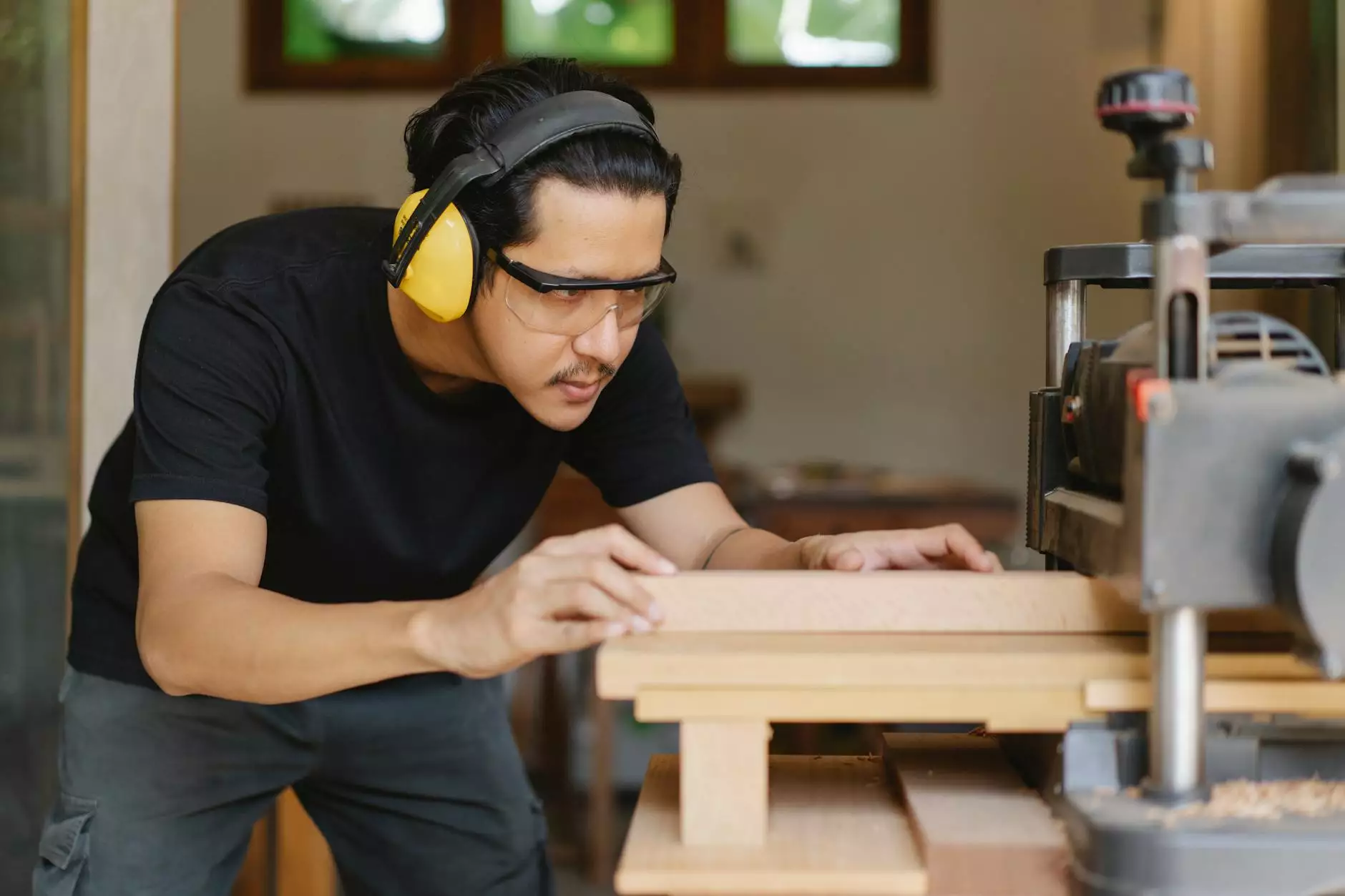
Metal cutting machines play a crucial role in various industries, providing precision and efficiency in the manufacturing process. From mechanical engineering to construction, understanding these machines can significantly enhance productivity and quality. In this comprehensive guide, we will explore the different types of metal cutting machines, their applications, and how to choose the right machine for your needs.
What Are Metal Cutting Machines?
Metal cutting machines are tools designed to cut metals into desired shapes and sizes. They utilize various mechanisms, including blade cuts, laser beams, plasma arcs, and more, to achieve accurate results. The effectiveness of these machines lies in their ability to handle various metal types, including steel, aluminum, copper, and alloys, making them indispensable in workshops and factories.
Types of Metal Cutting Machines
There are several types of metal cutting machines, each tailored to specific applications and materials. Let’s explore the most common types:
1. Band Saws
Band saws use a long, continuous band of metal with teeth to cut through various materials. They are favored for their ability to make precise cuts and are often used in construction and manufacturing environments.
2. CNC Machines
CNC (Computer Numerical Control) machines automate the cutting process with computer-guided precision. They are highly versatile and capable of creating complex shapes, making them essential in modern fabrication.
3. Laser Cutting Machines
Laser cutting machines use focused beams of light to melt or vaporize material. They are known for their precision, speed, and ability to cut intricate designs without the need for extensive tooling.
4. Plasma Cutters
Utilizing high-temperature plasma, these machines are ideal for cutting thick metals quickly. Plasma cutting is popular in automotive and aerospace industries due to its efficiency.
5. Waterjet Cutters
Waterjet cutters use high-pressure water mixed with abrasives to cut through metal. These machines can cut various materials, including glass and stone, and are known for their ability to create clean edges without thermal distortion.
6. Shearing Machines
Shearing machines make straight cuts in metal sheets. They are straightforward and effective for cutting thick, flat sheets of metal without producing waste.
Applications of Metal Cutting Machines
The applications of metal cutting machines are vast and varied, spanning numerous industries:
- Manufacturing: Used to produce parts and components for machinery and vehicles.
- Construction: Essential for preparing materials for buildings, bridges, and other structures.
- Aerospace: Used for crafting critical components in aircraft and spacecraft.
- Automotive: Important in fabricating parts like frames, panels, and engine components.
- Art and Design: Utilized by artists and craftsmen for creating sculptures and custom designs.
Choosing the Right Metal Cutting Machine
When selecting a metal cutting machine (máy cắt kim loại), consider the following factors to ensure you choose the best option for your needs:
1. Material Type
Different machines are suited for different materials. Ensure your machine can handle the specific metals you intend to cut.
2. Thickness of Materials
Know the maximum thickness your materials will have. Some machines excel in cutting thin sheets, while others are designed for thicker materials.
3. Precision Requirements
Depending on the application, you may need a machine that provides high precision. CNC and laser cutting machines are ideal for intricate designs.
4. Budget
Determine your budget before selecting a machine. While it's tempting to go for high-end models, there are many effective machines available at various price points.
5. Volume of Production
Evaluate the expected volume. For high-volume production, investing in a robust and fast machine will pay off in the long run.
6. Maintenance Needs
Consider the maintenance requirements of the machine. Some machines require regular upkeep, while others are low-maintenance.
Maintenance Tips for Metal Cutting Machines
Proper maintenance of metal cutting machines not only enhances their longevity but also ensures optimal performance. Here are some essential maintenance tips:
- Regular Cleaning: Keep the machine free from debris and metal shavings to prevent malfunctions.
- Check Blade and Tool Condition: Inspect for wear and tear and replace blades or tools as necessary.
- Lubrication: Regularly lubricate moving parts to reduce friction and wear.
- Calibration: Periodically calibrate the machine to maintain cutting accuracy.
- Electrical Checks: Regularly inspect electrical components to prevent failures.
Innovations in Metal Cutting Technology
The field of metal cutting continues to evolve with technological advancements. These innovations increase efficiency, accuracy, and sustainability:
1. Automation and Robotics
The integration of robotics in metal cutting processes improves speed and accuracy while reducing labor costs.
2. Advanced Software for CNC Machines
Modern CNC machines now come with sophisticated software that allows for complex design inputs, making programming easier and more intuitive.
3. Eco-Friendly Cutting Methods
New methods like waterjet cutting not only increase precision but also reduce waste and energy consumption, promoting environmentally friendly practices.
Conclusion
Understanding the landscape of metal cutting machines (máy cắt kim loại) is essential for businesses involved in manufacturing, construction, and various other industries. By selecting the right machine and maintaining it properly, you can elevate the quality of your output while enhancing operational efficiency. Explore the options available at DIY Home Depot and invest in the right equipment that meets your project needs.
may cat kim loai